From the Jobsite: Labesfal
ArmaFlex Ultima in Fresenius Kabi’s new penicillin production plant in Portugal
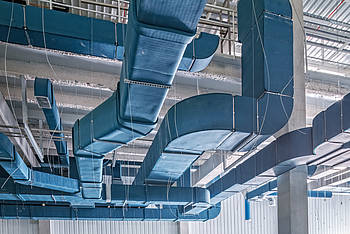
High-tech in the cleanroom
Premiere on the building site: even before it was officially launched, the new enhanced ArmaFlex Ultima had been installed in the new Labesfal - Fresenius Kabi plant. To prevent the pharmaceutical products manufactured here being contaminated, the construction materials have to meet the stringent requirements for cleanroom technology.
In the heart of Portugal, in Santiago de Besteiros, state-of-the-art production facilities for penicillin are currently being built. Labesfal S.A. is one of the top five generics producers in Portugal and since 2015 it has been part of the German Fresenius Kabi group. Fresenius Kabi is a global healthcare company that specializes in medicines and technologies for infusion, transfusion and clinical nutrition.
At the site in Santiago de Besteiros, the company produces capsules, tablets and liquid drugs in vials, ampoules and bottles, and sterile pharmaceutical powder. Located on the around 100,000 m2 site are not only three buildings with four independent production units, but also warehouse and logistics areas, quality control laboratories and offices for the administration. Following the 2014 investment in a new logistics platform, the plant is now being extended to include a new production unit with two lines for penicillin sterile powders for injection and infusion. In order to produce penicillin and cefalosporins at the same time, a completely separate building complex has to be available on the site. In this way the risk of cross-contamination between the two product groups can be ruled out.
Construction work started at the beginning of 2016. The new building will house facilities for producing batches and a high-speed manufacturing line for filling powder into glass vials aseptically. The cutting-edge technology will fulfil all relevant requirements of authorities throughout the world.
Good manufacturing practice (GMP) assures consistent quality
Quality control is of key importance in the pharmaceutical industry, because deviations in quality can have a direct impact on consumers’ health. High product quality is ensured by adhering to current GMP quality standards. These apply to the entire process from the analysis of starting materials, to IPCs (in-process controls) during manufacturing and the release of the finished products. A GMP-compliant quality management system ensures that the mandatory requirements of national and international health authorities are met. The Labesfal site has the facilities needed (e.g. climate chambers) to carry out stability studies in accordance with ICH ( International Council for Harmonisation of Technical Requirements for Pharmaceuticals for Human Use ) requirements.
Cleanroom technology prevents contamination
The building service equipment was designed by Spanish consultant engineers INDUS. This Barcelona-based company has a proven and highly successful track record in providing technical solutions for the pharmaceutical industry and other sectors with cleanroom requirements.
The cleanroom technology ensures consistently clean ambient conditions through filtered air. A key measure to minimize particle contamination is the generation of a laminar flow of particle-free air. The number of particles is controlled via the air flow, air humidity, air pressure and room temperature. To ensure that batches can be produced reliably, these parameters are continuously measured and recorded. The temperature, air humidity and pressure must be maintained at constant levels in order to provide comparable conditions and thus be able to control the number of particles reliably. The cleanroom, air-conditioning technology and adjoining areas form a complex, strictly monitored area. The design of the air-conditioning system and the use of filter-fan units or flow boxes, which ensure that the work surfaces are supplied with particle-free air, play a crucial role.
The various production areas and adjoining rooms are assigned to the appropriate cleanliness classes, which require that defined temperatures and air flows are maintained.
On both production lines a laminar air flow with a volume flow of 0.45 m/s ensures particle-free air. Thanks to this streamline flow, air enters the cleanroom vertically with little turbulence and prevents the sensitive working areas from being contaminated. The temperature on the production lines must be maintained at 18 ± 2 °C, the relative humidity must not exceed 20 %.
Huge cooling requirements
With outdoor temperatures of up to 33 °C in summer and a relative humidity of as much as 80 % in winter, the Labesfal plant has significant air-conditioning and ventilation requirements. Two huge cooling units with a cooling capacity of 565 kW and 11 air-conditioners with various capacities supply the new plant with cool air.
Responsibility for the cooling technology lay with Valtria Salas Limpas, Engenharia e Instalação, a company specialized in designing and installing cleanrooms and cleanroom areas from Madrid, Spain.
Smoke-free insulation material
INDUS specified the new ArmaFlex Ultima made by Armacell for insulating the galvanized-steel air-conditioning ducts. The first low-smoke insulation material fulfils the requirements of the Portuguese building code on fire safety in buildings (Decreto-Lei n.º 220/2008 – Segurança Contra Incêndio em Edifícios). According to the building code, thermal insulation materials installed on air-distribution ducts must achieve at least fire class BL-s2,d0. In comparison to a standard elastomeric product, ArmaFlex Ultima exhibits 10 times less smoke. The foam, which is based on the patented Armaprene technology, is the first elastomeric insulation material in the world to achieve B/BL-s1,d0 – the best fire class for organic building materials.
All the ventilation ducts were insulated, except for the exhaust-air ducts, which carry the “used” air out of the building. To prevent condensation and energy losses, the cold supply-air ducts were insulated with 25 mm thick sheets. On the warm extract-air ducts sheets in a thickness of 19 mm were installed.
A team of six to eight employees from the insulation firm Martins Oliveira - Isolamentos Industriais from Fátima began with the insulation work at the beginning of August and it should be completed in November. Not only air-conditioning ducts and ventilation pipes with diameters ranging from 125 to 710 mm, but also the filter boxes were insulated with ArmaFlex Ultima. All in all the insulators installed 1,200 m2 of ArmaFlex Ultima sheets in an insulation thickness of 19 mm, 1,500 m2 in 25 mm and 100 m² in 9 mm thicknesses. Some of the material installed was self-adhesive; in the case of fitting covers the ArmaFlex Ultima sheets where fully glued using the ArmaFlex Ultima 700 adhesive. Managing Director Basílio Oliveira’s verdict: “ArmaFlex Ultima is even easier to install than other ArmaFlex insulation materials. The colleagues were very satisfied with the ArmaFlex Ultima 700 adhesive, too.” The insulation materials and the ArmaFlex Ultima 700 adhesive were delivered by Distriplac Portugal - Comércio de Isolamentos.